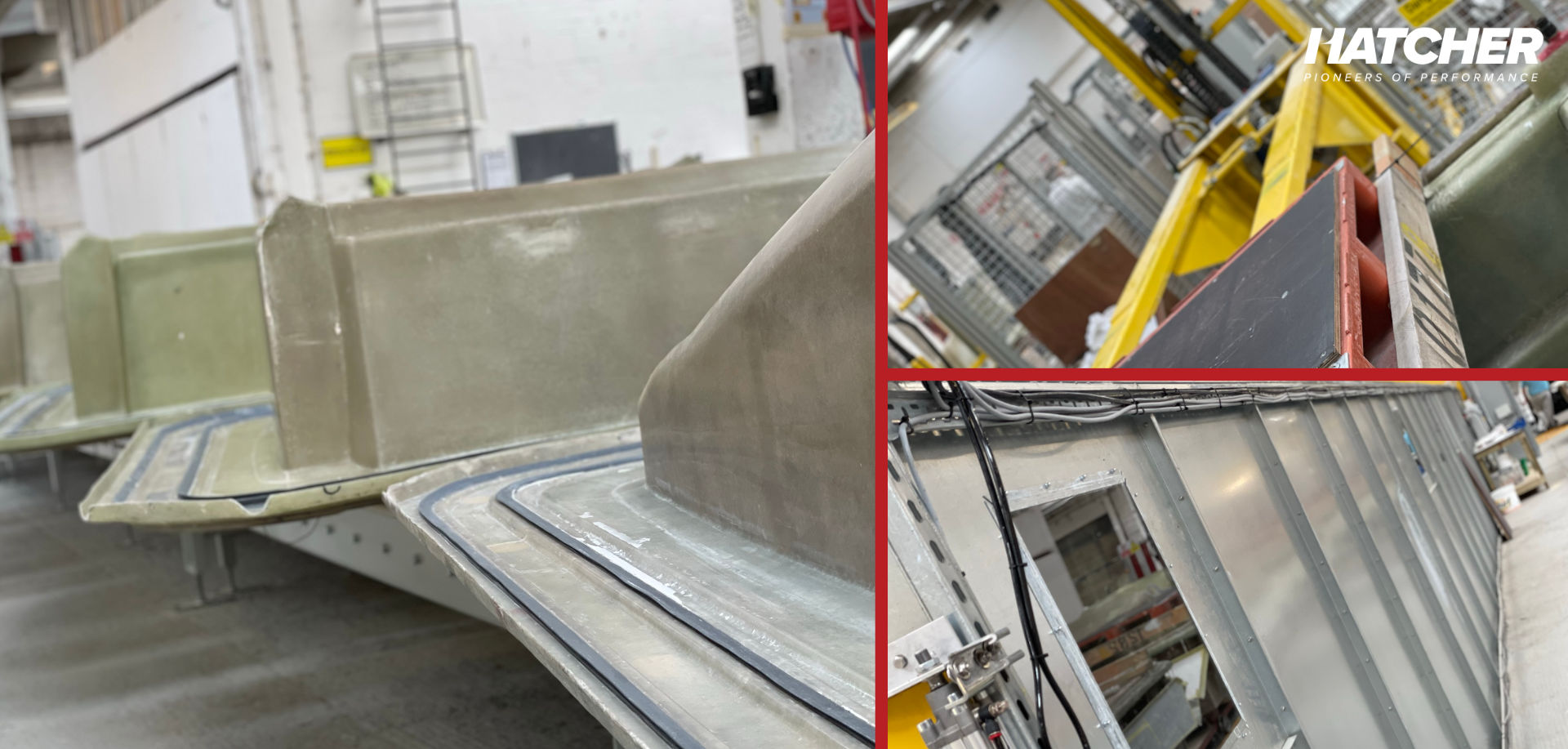
Improving efficiency through innovation
Necessity is the mother of all invention so they say – and what could be more necessary, in the current climate, than saving fuel and improving the efficiency of transportation and road freight.
No stranger to innovation, Hatcher Components Ltd, have seen a surge in demand with the rise of the cost of fuel. Established in 1968, Hatcher pioneered, developed and manufactured aerodynamic enhancements for commercial vehicles and have led the market ever since.
The shape of most goods vehicles is far from streamlined, since the design of the vehicles is governed more by other considerations, such as ease of load handling, maximising the load size within legal constraints and ease of maintenance.
The aerodynamic drag coefficient of a moving vehicle has a considerable effect on fuel consumption, particularly when driving at motorway speeds. For a typical commercial vehicle at a speed of 60 mph, nearly half the power of the engine is used just to overcome aerodynamic wind resistance. Couple that with the complications of powering refrigeration units and the running costs continue to mount up.
To combat this, Hatcher developed a range of spoiler kits to suit most HGV and LGV cabs, fixed or fully adjustable to cover any load eventuality. There is a separate range fully devoted to refrigerated vehicles designed not only to enhance the aerodynamics, but to enhance airflow to the fridge units themselves thereby improving overall efficiency for the vehicle.
To meet the increase in demand, Hatcher have commissioned a state-of-the art production line, at their Framlingham facility, enabling them to equip complete fleets in record time. By implementing the new line, Hatcher were able to invest in the latest in temperature control and resin injection technology. This means that only the exact amount of resin is applied to each product, reducing wastage, and is cured under optimum conditions.
Scott Parish, Operations Manager for Hatcher said, “As demand increased, the call for shorter lead times also increased. So, it was inevitable that we had to make substantial changes to our methodology in order to keep customers happy. Before the production line was commissioned, we could only produce one part per mould per day and although we have a lot of moulds, this still meant a lot of time for curing. The new line means we are able to increase production and improve our lead times without sacrificing quality.”
Their spray booths and trimming shops have also been upgraded and the whole workshop re-aligned to improve flow. To further enhance product flow, fully bespoke robots have been installed at each end to remove and turn the moulds, as well as an automated tracked trolley system to move the parts down the line at various stages. By installing this line, Hatcher are now able to produce a fully cured part every eight minutes. From a customer’s perspective it means that their parts are now more consistent, with no sacrifice to quality over speed.
MD Matt Herbert is delighted with the new line, and the improvement to overall efficiency. “Fleet management, and transportation in general is becoming exponentially more expensive and we feel that pain too. Our team have done a fantastic job installing and implementing the new line. As a result, we are now more efficient, our footprint is smaller and we’ve improved on product quality. This means our customers can equip larger fleets faster than ever before, thereby gaining the fuel-saving benefits as quickly as possible”.