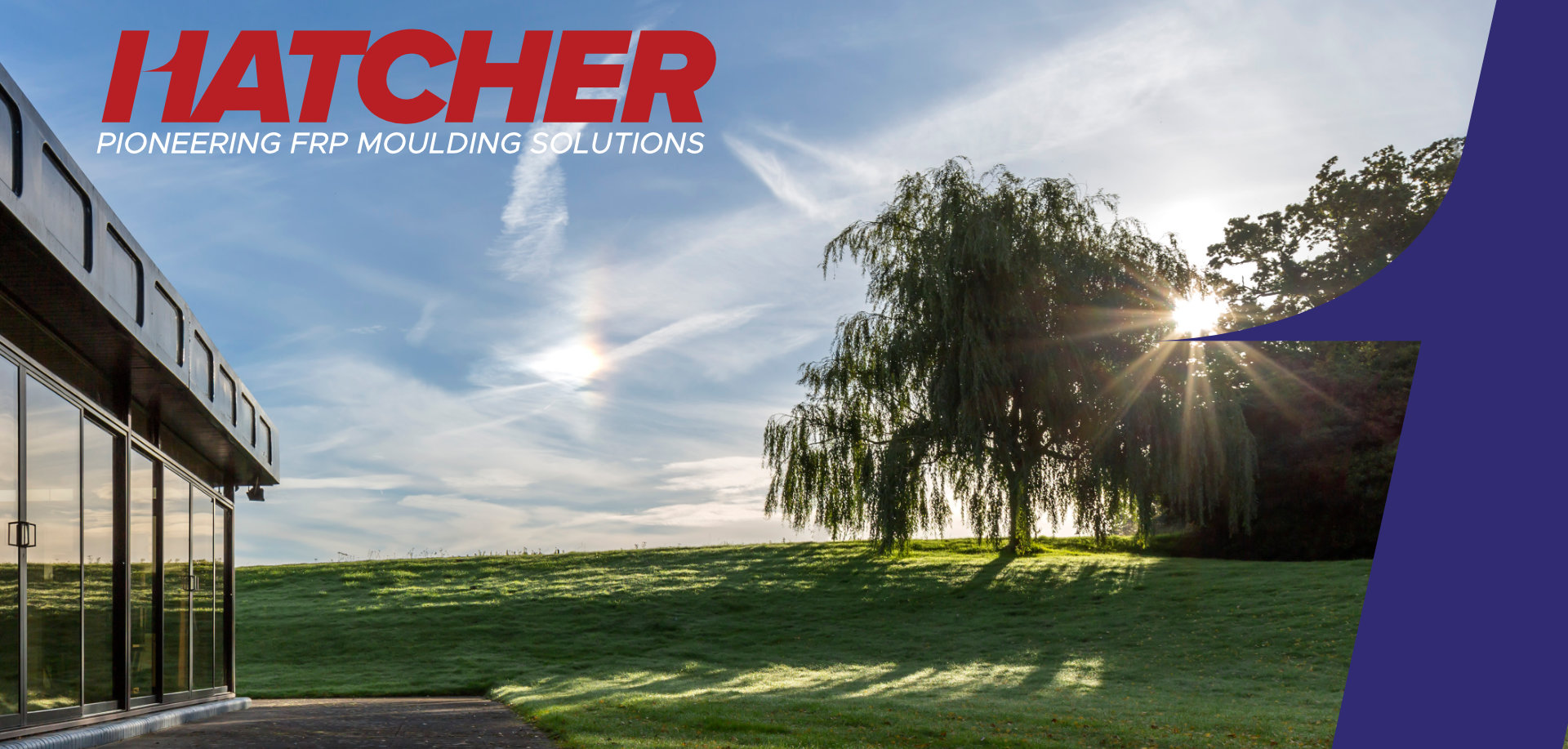
CONCEPTION | DESIGN | REALISATION
With an established background designing and manufacturing bespoke parts for the commercial vehicle market including as a Tier#1 supplier to OEMS, Hatcher’s facilities in Framlingham are configured to offer contracted design, moulding and manufacturing from the ground up.
We offer a complete in-house design for manufacture and tooling service. We can quickly and efficiently produce parts from either existing tooling or scratch-build tools to suit your requirements.
Our highly trained and experienced team of engineers utilising the latest: CAD, 3D scanning, 3D Printing, CNC machining can manage projects from conception through to completion, overseen by a dedicated project manager to help you along the way.
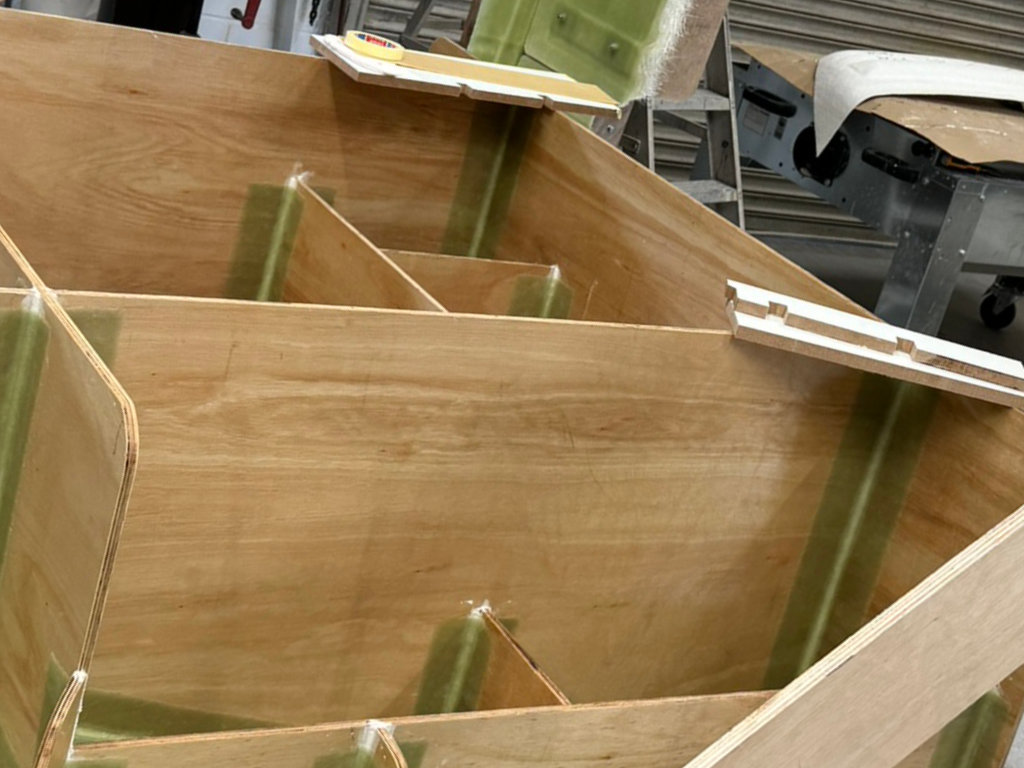
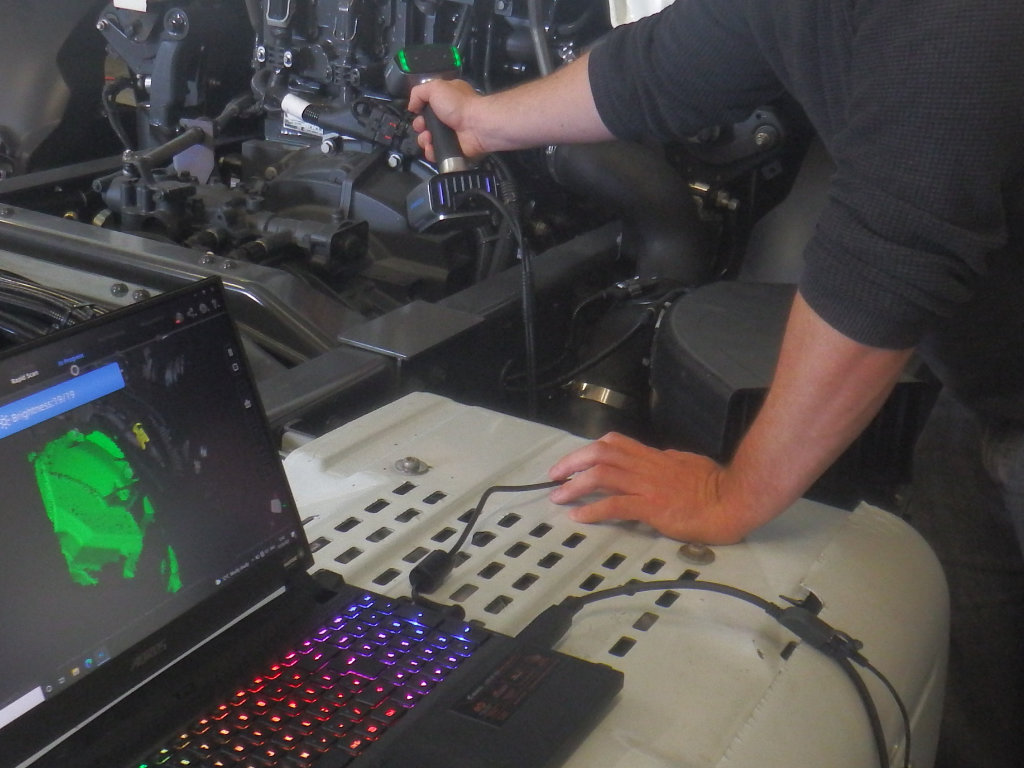
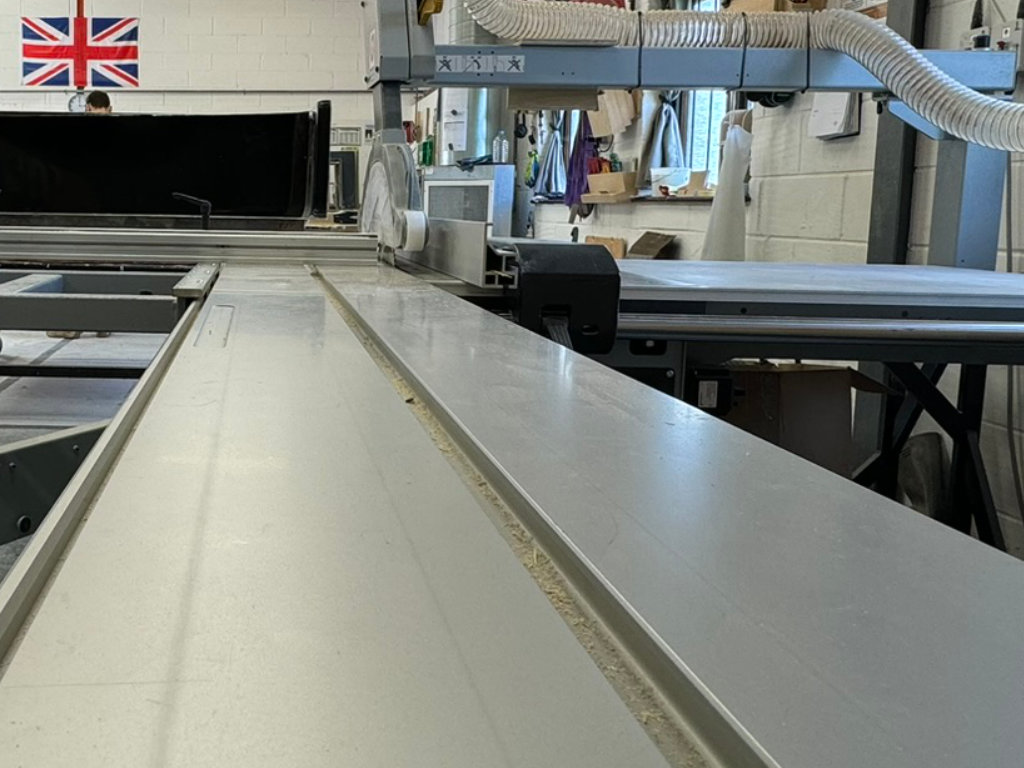
“The quality of workmanship is impeccable and the overall service we have received has been exemplary throughout the project” - Unisurge
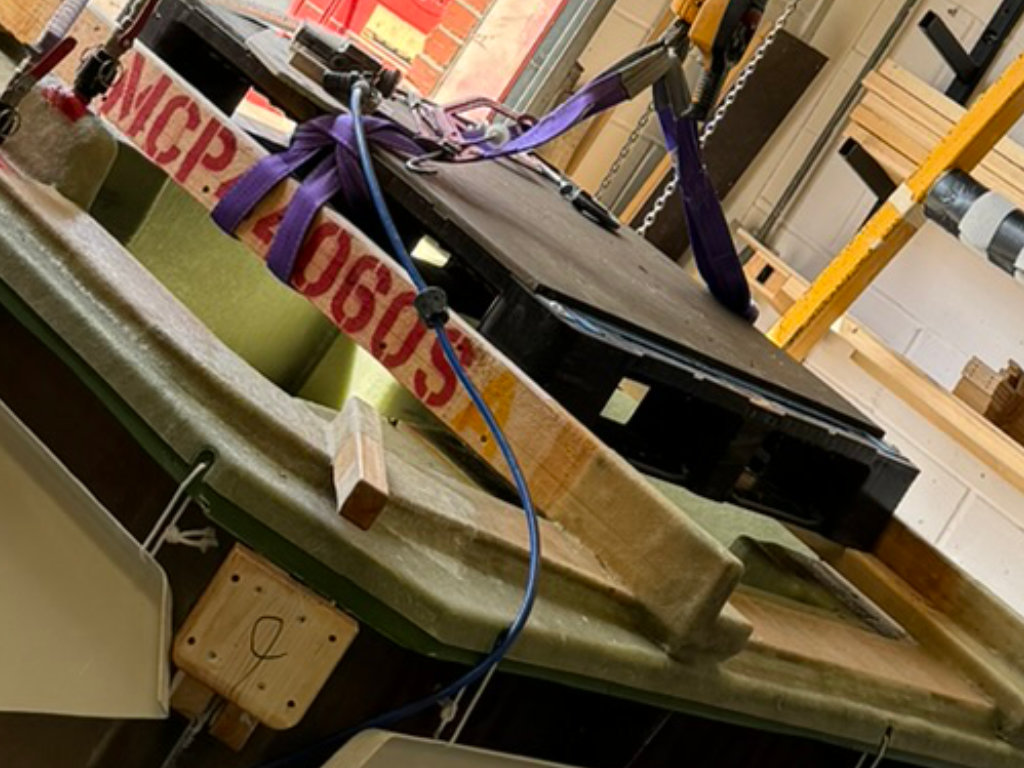
FLEXIBLE | EFFICIENT | CONSISTENT
At Hatcher we use numerous moulding methods such as Hand Lay-up, Spray Lay-up and light RTM which caters for wide variations in part geometry and volume.
Our workshop and facilities have been recently been upgraded and re-configured to promote workflow with improved productivity.
Our expertly designed tools are made from premium materials to provide longevity and consistency.
Wherever possible we adopt multi-cavity tools for increased output, saving both time and money for larger orders.
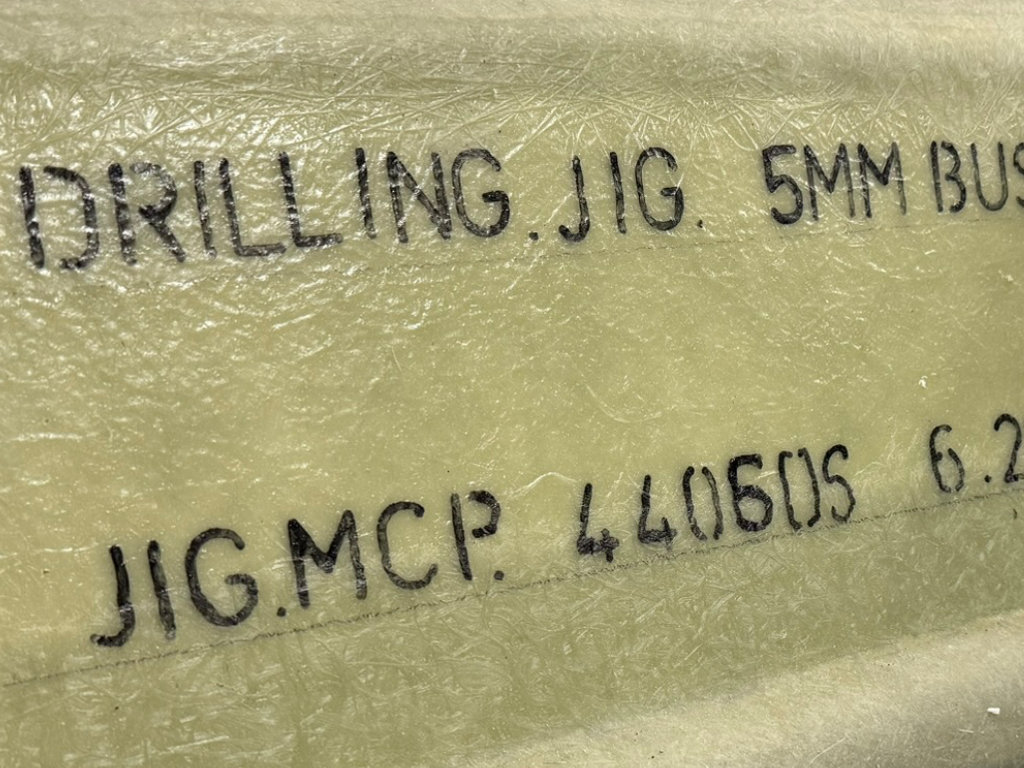
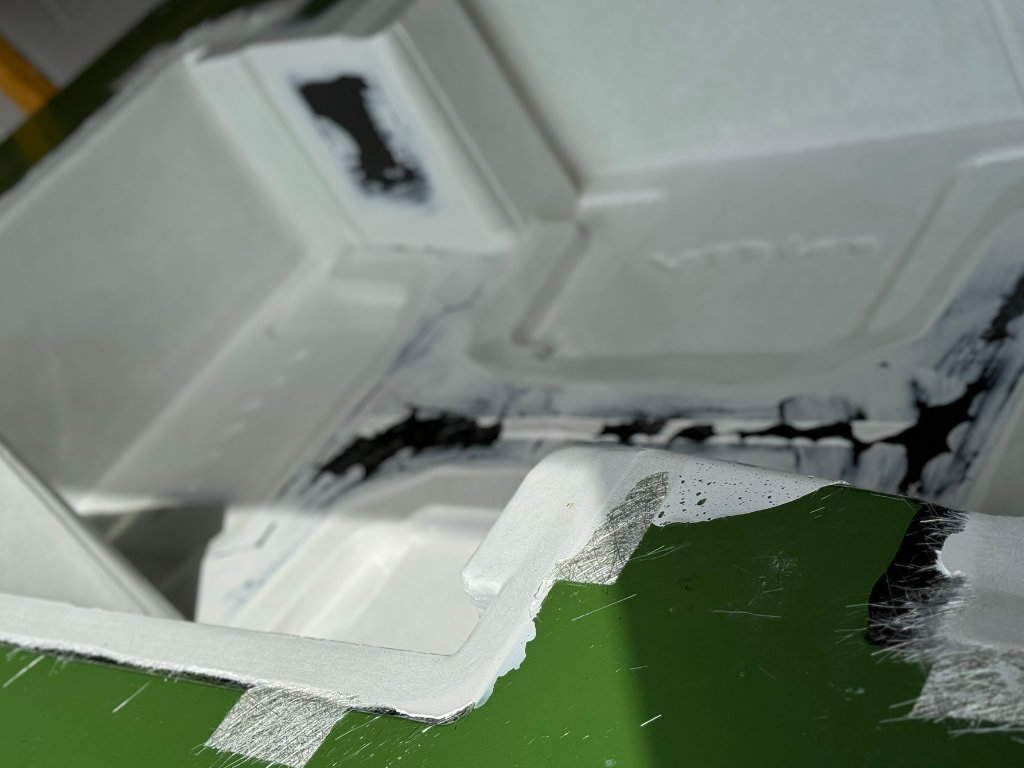
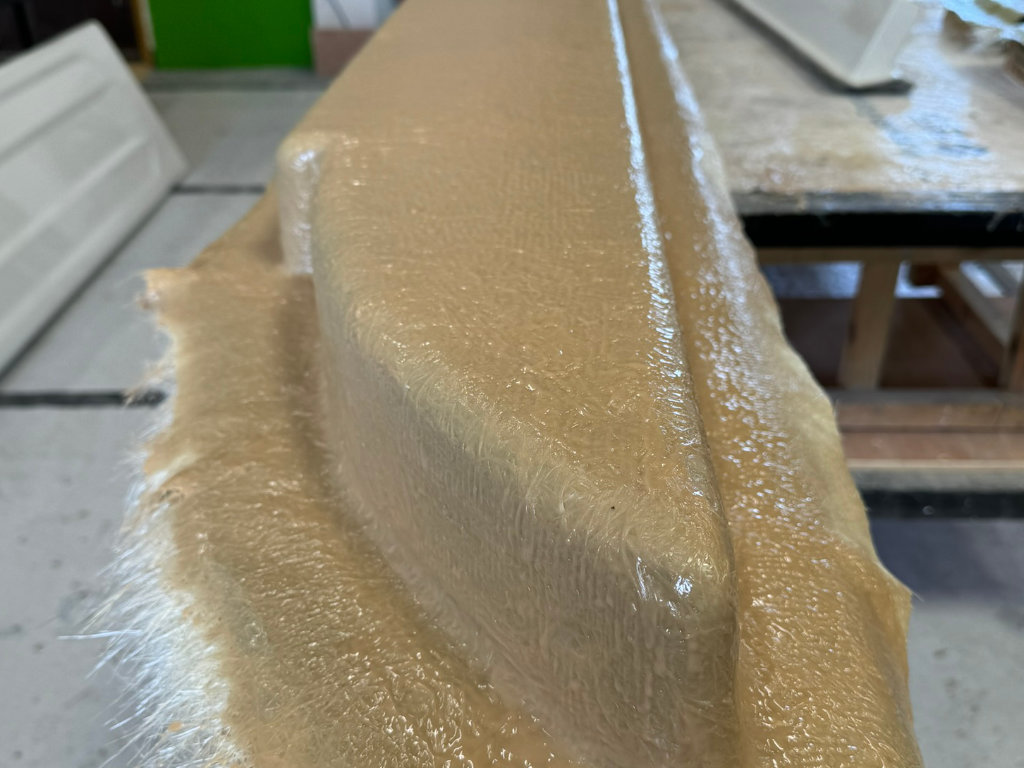
UNIQUE SEMI-AUTOMATED FRP PRODUCTION LINE
Hatcher have installed a bespoke state-of-the-art mould tool handling system integrated into a unique semi-automated production line, enabling us to provide increased throughput of parts in record time.
Our new line includes the latest in temperature control and resin dispensing technology. This means that exacting amounts of materials are utilised for every product, resulting in consistent part specifications, reduced waste, and finite process times.
To further enhance product flow, fully bespoke robots open, close and turn the moulds integrated with an automated tracked trolley system to move the parts down the line at timed intervals. By installing this line, we can now produce a fully cured part every eight minutes. Ordinarily, using standard methods, output would be one to two parts, per tool, per work shift.
This unique facility allows for larger volumes of parts to be consistently produced with no sacrifice to quality for speed and with all the benefits derived from matched closed tooling.
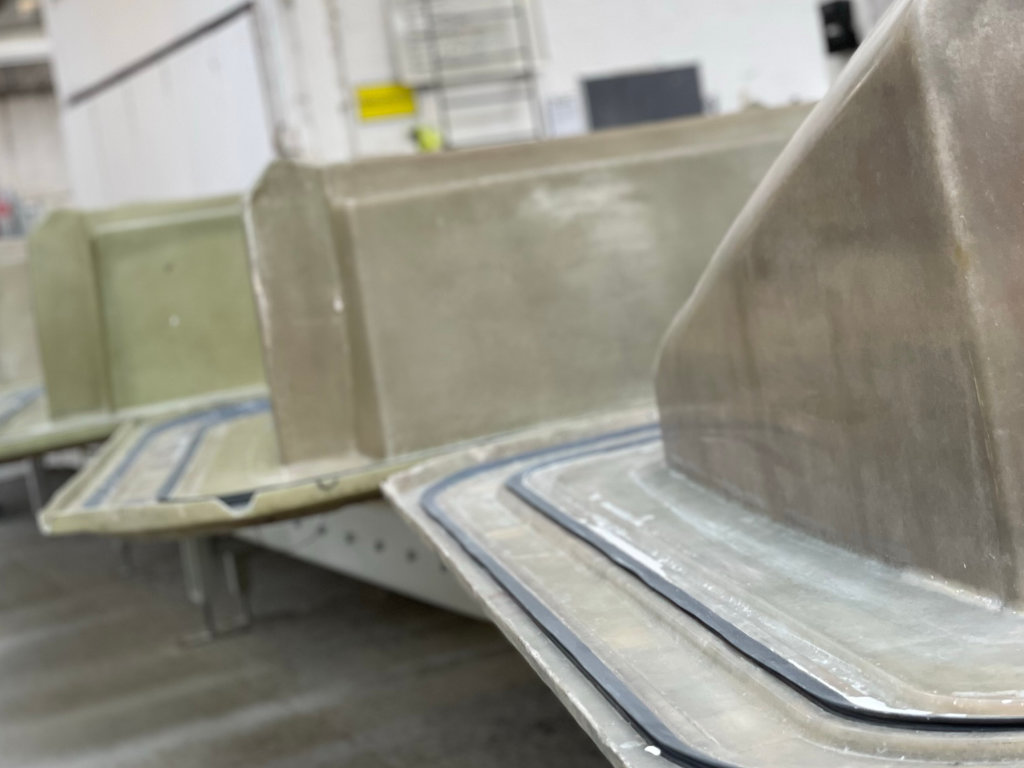
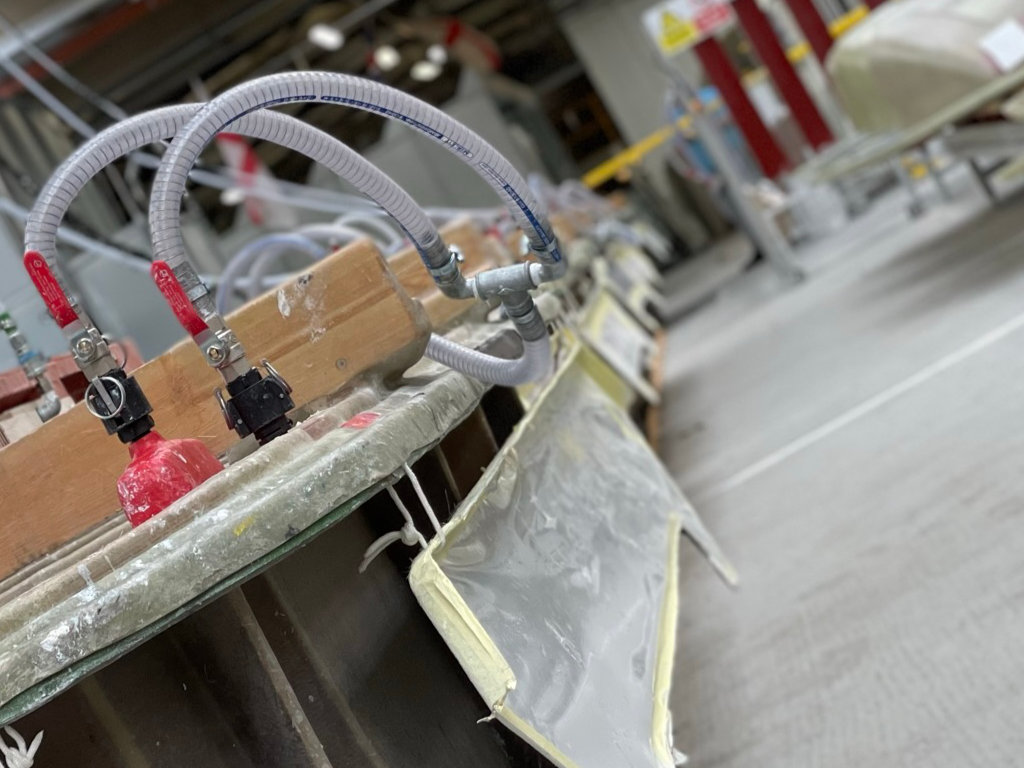
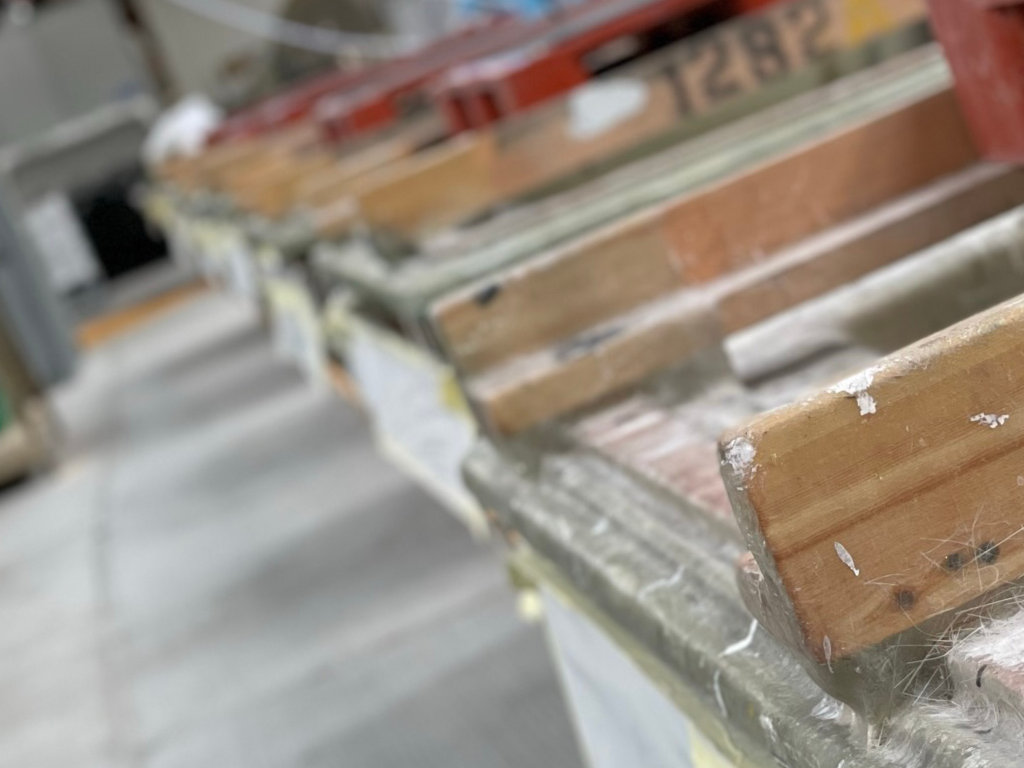
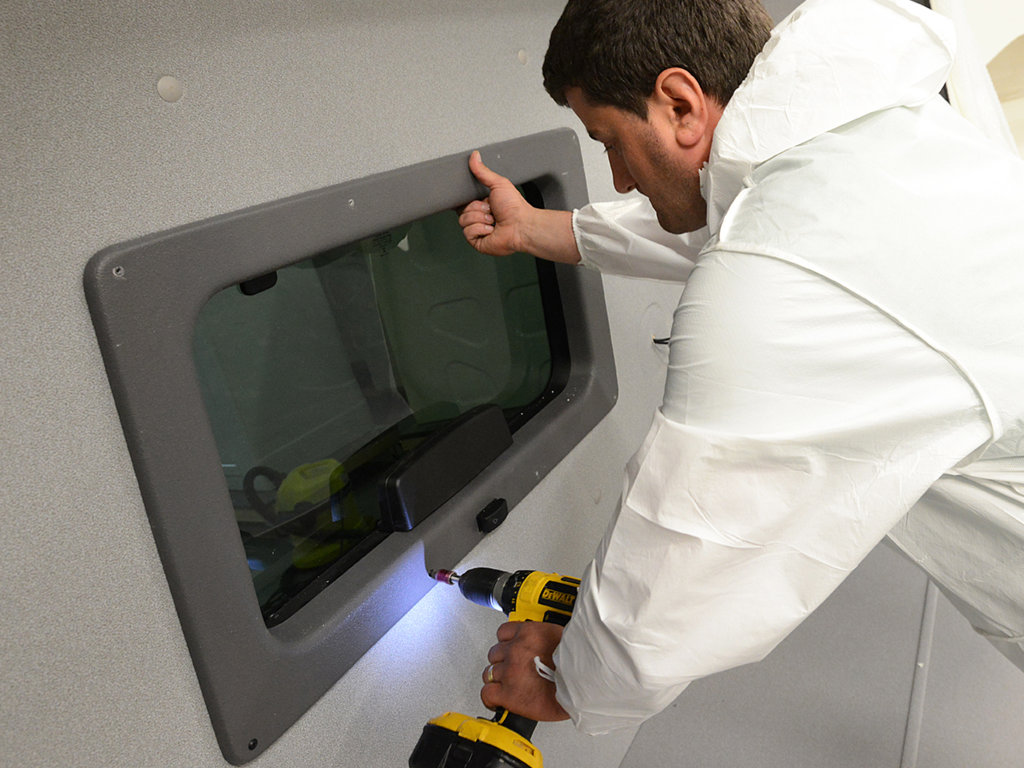
QUALITY | PRECISION | READY-TO-FIT
It may be that a quality finished part is all that is required. At Hatcher, we’re able to go way beyond this.
We have a team of expert finishers, trimmers and assemblers in place to ensure that your part is ready to go as soon as it arrives.
With our commercial vehicle experience on board, we also have auto electricians, fabricators, upholsterers and fitters available to cover any requirement you may have.
All parts are made in accordance with our ISO 9001 certified quality management system, so you can be assured your products will be consistently finished to an impeccable standard.
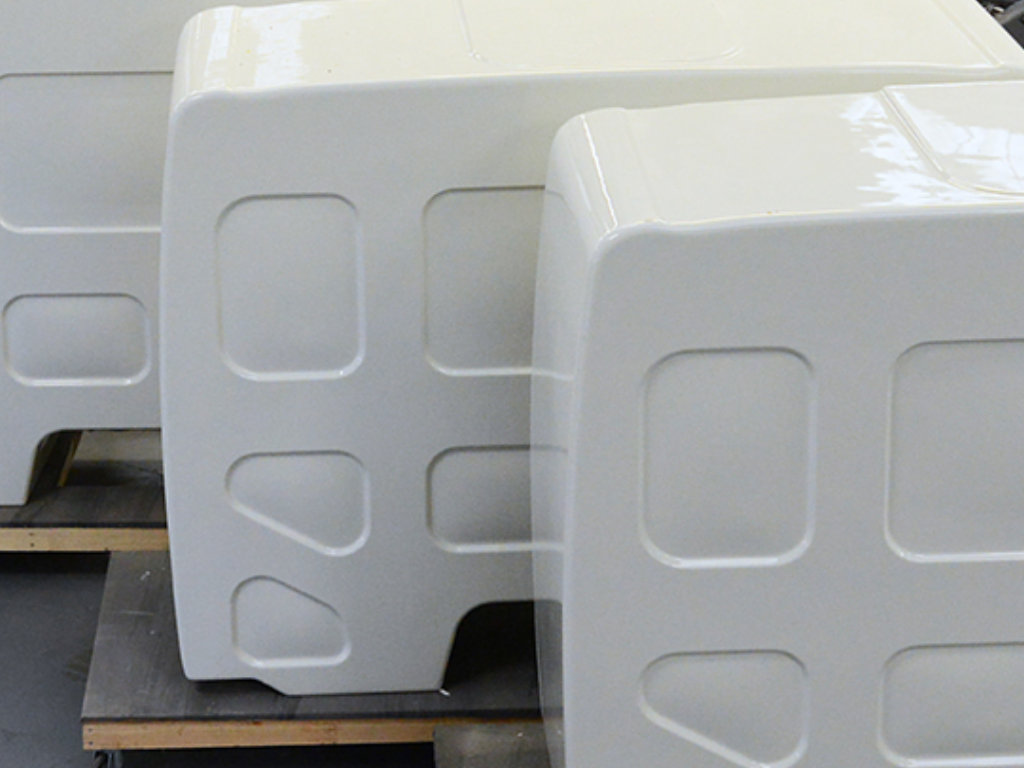
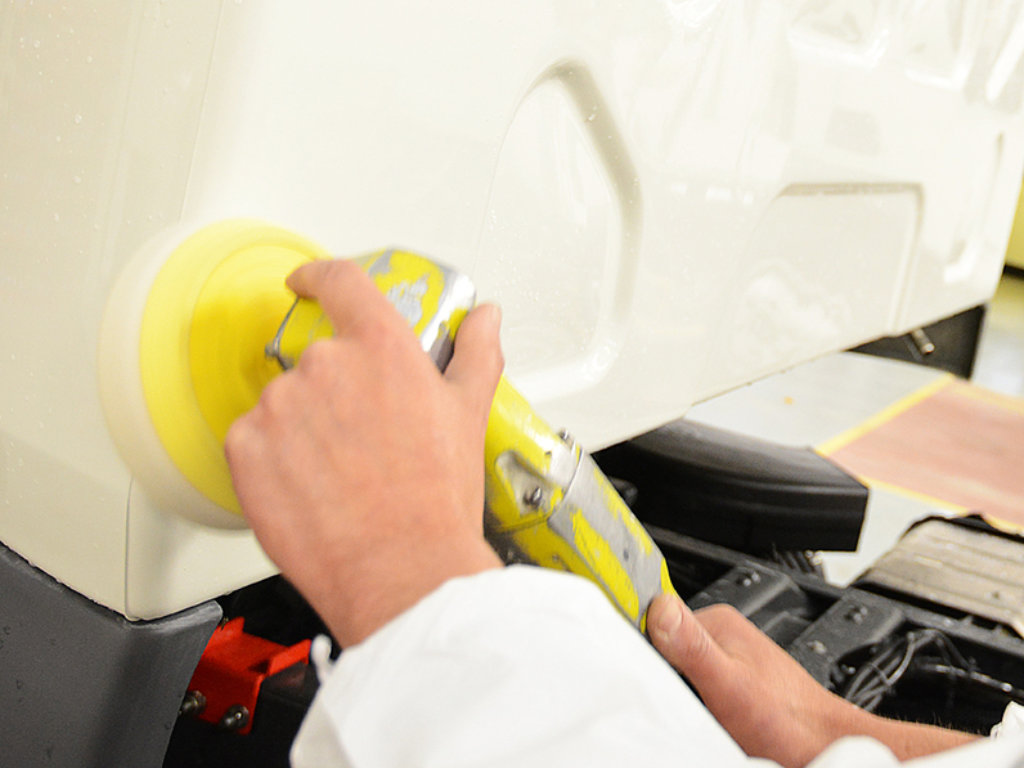
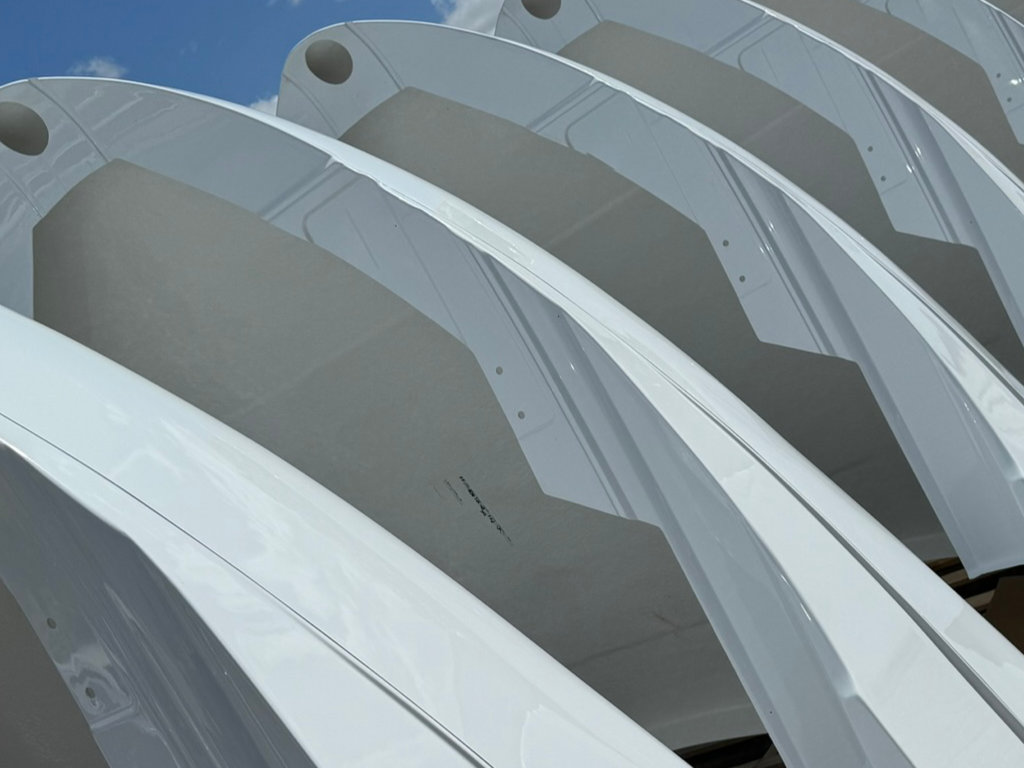
How can we help?
Thanks to a highly skilled and experienced workforce, Hatcher have a proven track record in delivering pioneering product innovation and high performance, cost-effective mouldings. As a trusted partner to OEMS, Hatcher could not be better placed to handle your moulding requirements whether they’re large or small.